Ma Hailong, Zhao Yantao, Shandong Mining Machinery Maike Building Material Machinery Co., Ltd.
1 Introduction
Industrial control computer technology has provided a complete set of automatic control solutions for the development of industrial automation, information and national defense security in China, and has promoted the rapid development of China's national economy. At the same time, it also played a positive role in promoting the replacement of industrial control technology. With the increasing application of computer technology in the field of industrial control, the development prospects of industrial control computer technology will be very broad.
The Industrial Personal Computer (IPC) is a ruggedized enhanced personal computer that can function reliably as an industrial controller in an industrial environment.
Compared with ordinary computers, it has the following features:
1) The chassis is made of steel structure and has strong antimagnetic, dustproof and anti-impact capabilities.
2) A dedicated backplane is used in the chassis, and the backplane is configured with high-strength PCI and ISA slots.
3) A special power supply is installed inside the chassis. The power supply has strong anti-jamming capability.
4) Has continuous working capability for a long time.
The IPC has the same good man-machine interface as the computer. Compared with PLC, it has the following features:
1) Has a good design and application interface. Its operation and application is superior to a single menu-driven mode.
2) With multithreading and multitasking. Satisfy the more complex multi-tasking system control requirements in the current industry.
At present, most of the cutting and transporting systems use PLC to control. The operation of the equipment through the console and touch screen has a low degree of visualization. With the improvement of the visualization, especially the man-machine interface requirements, the use of IPCs for control will become inevitable.
Based on this, we have made improvements and upgrades to the traditional control system of the cut-off transport, replacing the original PLC control with the control of the industrial computer. Expand its control capacity, improve compatibility and anti-jamming capabilities, and add new features to make it have a good man-machine interface to better meet customer needs.
2ã€Introduction of IPC Control System
The industrial control machine cutting and conveying control system integrates data acquisition, processing and control into one, and is programmed as special control software. This software has a high degree of intelligence and a built-in voice alarm function. It can report the source and cause of equipment failures within the first time, effectively shortening the time for fault maintenance. At the same time, it has a good human-machine interface and action demonstration functions to meet customers. The need for visual operations. The system architecture is shown in Figure 1.
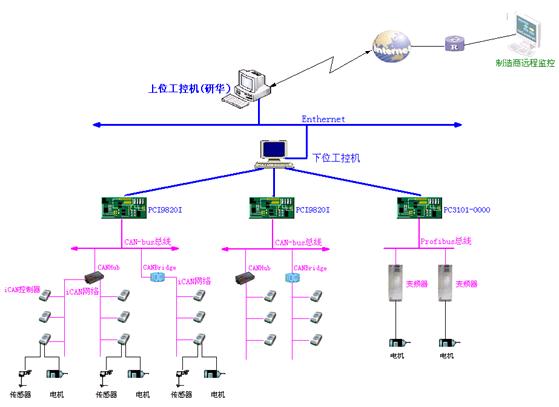
Figure 1 System Architecture
The system consists of factory management level and field level. The factory management level consists of a control computer and a monitoring computer, and a local area network is formed by Ethernet and field-level industrial control computers. Relying on management computer wincc monitoring software and ERP management software, real-time monitoring and scheduling on site. The field level consists of a lower IPC, a communication module, a signal acquisition and transmission module, a precision sensor, and a servo controller. The lower IPC connects the IPC to the inverter, encoder and robot through profibus protocol to realize the setting of the transmission speed, the determination of the brick group position and the given position of the brick stacking position; through the CAN bus protocol and detection elements, Actuator connection to achieve signal acquisition and control instructions sent.
3, the main features of IPC control system
3.1 Intelligent
The system has comprehensively used computer network technology, intelligent control technology, and automation technology to realize intelligent and automatic management of production processes. Specifically embodied in:
1) Fully automated production process
After the operator sets the production parameters on the master machine and issues the production instructions, the master machine automatically analyzes the production parameters and generates the corresponding hierarchical control instructions, which are issued to each subsystem. Under the management and scheduling of the master computer, the entire production line is fully automated without human intervention.
2) Troubleshooting Automation
â—† Automatic detection of equipment failure.
â—† Most failures can automatically enable standby devices online to avoid downtime.
â—† A small number of faults that require manual intervention, automatic alarm (voice, screen prompts), SMS notification.
3.2 Modularization
The whole system is divided into host control module, cutting module, loading and unloading module, code blank module and so on. Each module maintains a high degree of independence and communicates with each other through standard interfaces. This facilitates separate management, upgrade, and maintenance of each module, and also simplifies the process of equipment installation and commissioning.
3.3 Networking
1) In the system structure, the on-site level and the factory management level form a local area network to achieve centralized control, monitoring and scheduling of the system.
2) The manufacturer connects to the customer's equipment through the VPN. The technical personnel can remotely retrieve the equipment running logs, configuration parameters, and other technical documents on the customer's equipment to remotely maintain the customer's equipment.
4ã€The main functions of the IPC control system
In addition to being compatible with the functions of the PLC control system, this system has added user management functions, mutual inspection functions between devices, voice alarm functions, online display of work operations, remote debugging functions, operation log viewing functions, and system help. The main interface of the system is shown in Figure 2.
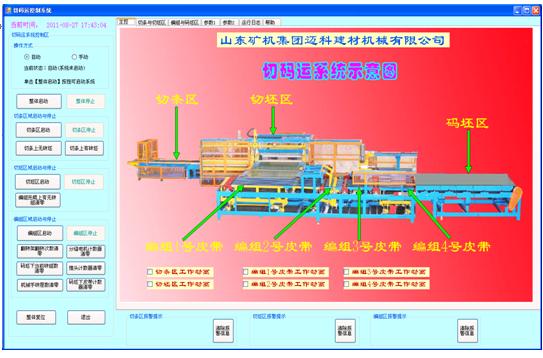
Figure II system main interface
4.1 User Management Functions
To achieve the system's security management, we must first solve the operator's identity problem, and then carry out the necessary business authorization work. According to the operation authority, the system divides the operator into the administrator and the general operator. The administrator has the highest administrative rights and can view all the functions of the system, including adding, deleting, modifying, and viewing the startup logs of ordinary operators. The ordinary operator has the most basic operating authority and can only perform daily equipment operations and maintenance, such as the system. Start and stop, manual debugging and so on. The user management interface is shown in Figure 3.
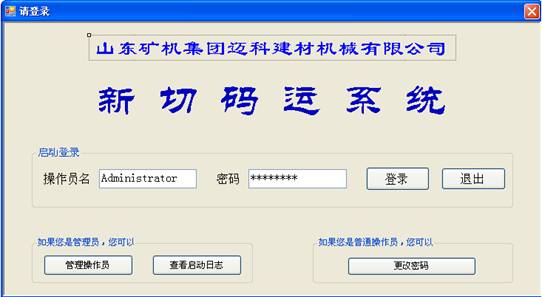
Figure 3 user login screen
4.2 Work Run Online Display Function
In order to maximize the user's intuitive control over the operation of the cut-off transport equipment, we have added an online display function of the cut-off transport equipment. This function can visually display the real-time running status of a certain area and the current working status of the equipment. After the device is started, select an area to view the immediate operating status of the device in the area. Taking the No. 3 aircraft in the marshalling area as an example, the effect is shown in Fig. 4.
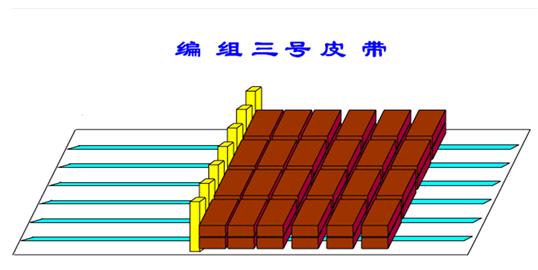
Figure four animation effect screenshot
4.3 Inter-device mutual check function
In order to ensure that the bricks are accurately disposed, the detection of signals is very important. Ensuring the normal operation of the sensor is a necessary prerequisite for the normal operation of the equipment. There are two methods of detecting the normal operation of the sensor. One is to rely on hardware to implement self-test of the device; the other is to rely on software to logically implement device interlocking. To save costs, we rely on software. Specifically embodied as follows: relying on dedicated software to manage two adjacent sensors, the signal sequence through the first sensor, after a set period of time, the system will automatically detect the second sensor, determine whether the signal is right or wrong, according to this instruction , adjust the equipment operating status.
4.4 Voice Alarm and Online Display Function
During the entire operation of the equipment, the system monitors the equipment in real time. When the system fails, the alarm function starts. The voice informs the user of the source of the fault and writes the cause of the fault to the log file. At the same time, the system automatically enables the device standby settings to avoid downtime and ensure the smooth operation of the device. After the user passes the voice security alert, the device failure is rectified and the personal safety of the maintenance personnel is ensured.
4.5 Running Logging Function
With the ever-increasing wealth of modern software technologies, it has become impossible to completely eliminate bugs in software. Therefore, timely detection of errors, locating faulty site information, and quickly eliminating software errors are very important tasks, even in the actual software operating environment. The software running log is an important means to capture the wrong site information.
The operation log will record the starting and stopping time of the equipment, the operation and alarm conditions of each equipment component. After the device is started, the running log recording function starts. Users can choose to view the current running status of a certain device, or select to view past records. The interface is shown in Figure 5.
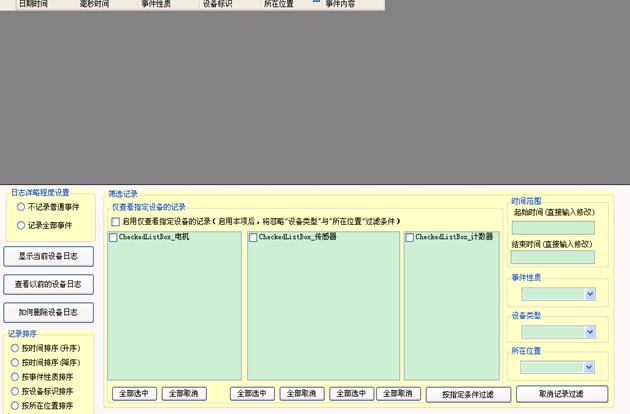
Figure 5 running log query interface
4.6 Remote debugging
With the rapid development of network technology and computer technology, the Internet has become an integral part of our work and life. The development of networking has made it possible to debug at different locations. With the customer's permission, the manufacturer can network with the industrial IPC through the VPN virtual LAN to obtain the equipment operation log and check the working status of the equipment. It can quickly and accurately understand and solve the problems encountered by the system, reduce service costs, shorten maintenance time, and increase business efficiency.
5, the future of industrial computer technology applications
The application of IPC has infiltrated into every area of ​​people's life. With the further expansion of the scope of application of the IPC industry, it is bound to go beyond the scope of industrial applications. By 2020, China will use the realization of informatization to lead the country toward modernization. During the period, industrial control computer technology will usher in good opportunities for development, and the commercialization of IPC technology will have a very broad prospect. With CompactPCI bus technology as the core, the new generation of IPC technology covering CompactPCI, PXI and ATCA will surely lead the trend of this era.
Gasoline Generator,Fule Tank Generator Set,Silent Trailer Diesel Generator,Small Diesel Power Generator
XCMG E-Commerce Inc. , https://www.xcmg-generator.com