1 Overview
Intelligent servo technology is an emerging mechatronics technology in recent years. It is formed on the basis of traditional servo drive technology, and integrates a variety of modern control technologies such as motion control technology, DSP technology, PLC technology, field bus technology and so on. Intelligent servo products have the characteristics of intelligence, networking, modularization, digitalization, etc., and are the future development direction of servo technology.
The iPack2000 multi-axis servo pillow packaging machine control system introduced in this paper is based on the iDrive intelligent servo independently developed by China, and replaces the traditional PLC + servo drive solution with an integrated and highly integrated intelligent servo solution. iDrive intelligent servo controller has built-in electronic cam and color mark capture and compensation functions, compatible with hot cutting and cold cutting processes, and realizes dual-axis synchronization through the bottom of the servo drive system.The system responds quickly and the synchronization accuracy is high. Servo solution reduced by 40%. The driver can communicate directly with the HMI, which greatly enhances the simplicity of the control system and reduces the time required for device debugging.
2. Comparison of traditional pulse-based system and intelligent servo system
Figure 1 and Figure 2 show the comparison of the traditional PLC + servo drive system and the structure of the iPack2000 system using an intelligent servo controller.
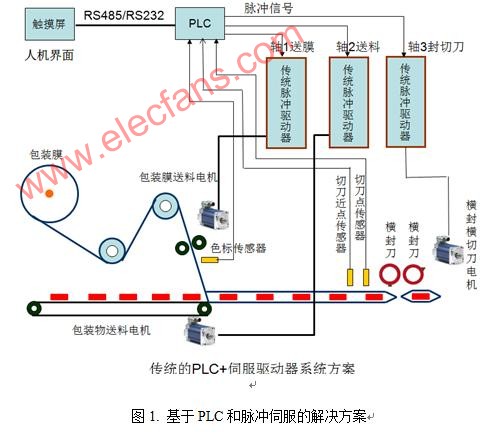
Figure 1. Solutions based on PLC and pulse servo
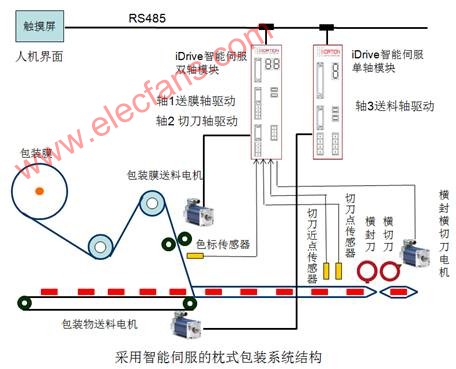
Figure 2. Intelligent servo-based solution
As can be seen from the comparison between Figure 1 and Figure 2, the intelligent servo control scheme uses a built-in controller instead of PLC, which realizes the synchronization of two axes (cutter axis and film feed axis) and electronic cam inside a dual-axis iDrive intelligent drive Relationship, color scale compensation is also completed inside the same intelligent servo controller, the system response is greatly improved, the system structure is simplified, and the cost is significantly reduced. At the same time, due to the bus-type structure, the system solution using intelligent servo is more flexible and can be easily changed to a dual-axis system or a four-axis or even multi-axis system.
3. Pillow packaging solution of intelligent servo system with built-in electronic cam
The three-axis servo pillow packaging machine control system shown in FIG. 2 is taken as an example to describe each part of the system. The lateral sealing and cutting method of the pillow packaging machine is heat sealing and cold cutting, that is, heat sealing is performed first, and then cross cutting is performed. The system can also be easily set up and is compatible with common heat sealing and cutting processes. During the operation of the equipment, the running speed of the transverse sealing and transverse cutter is kept at a constant speed (hereinafter referred to as the driving shaft), the speed of the film feeding shaft (hereinafter referred to as the driven shaft) runs in a cam relationship, and color scale compensation is introduced. The function of the cam is to ensure that the movement of the film feeding shaft and the movement of the transverse sealing knife and the transverse cutting knife at the cutting point are strictly synchronized during the transverse sealing and transverse cutting. The feeding shaft is strictly synchronized with the actual speed and position of the film feeding shaft. The introduction of the cutter near-point sensor signal is set at the request of a pillow packaging machine manufacturer, the purpose is to prevent false detection of the color mark signal. This function can also be implemented in software within the system without introducing sensor signals.
3.1 Process flow
The packaging is sent into the packaging film through the feeding mechanism, and the vertical sealing operation is completed first; then the contents continue to advance in the packaging film after the vertical sealing, enter the horizontal sealing and cross cutting process, and complete the horizontal sealing and cross cutting, and finally become the finished product .
3.2 System block diagram
As shown in Figure 3, the system has three servo axes. A dual-axis iDrive intelligent servo and a single-axis intelligent servo are controlled by RS485 bus. The dual-axis iDrive serves as the main controller. The two servo drive modules built into the dual-axis iDrive are used to control the horizontal sealing (cross-cutting) knife axis and film feeding axis, and the single-axis iDrive controls the feeding axis. Among them, the driven axis (that is, the film feeding axis) follows the driving axis (cross seal cross axis) with the set electronic cam to ensure the strict synchronization of the cross seal cross cut. At the same time, the follower axis is detected according to the position detected by the color mark signal The compensation signal compensates the position of the driven axis, and the feed axis keeps in full synchronization with the movement according to the actual position of the driven axis. The cutter signal and color mark signal in the I / O signal are directly connected to the I / O interface of the dual-axis iDrive. The control signal of the Jog motion mode is also connected to the I / O port of the dual-axis iDrive, including two motion mode control switches for forward movement and backward movement of the slave axis for debugging. Figure 4 shows the interface of the servo system and the assignment of the master and slave axes.
SHAPE \ * MERGEFORMAT
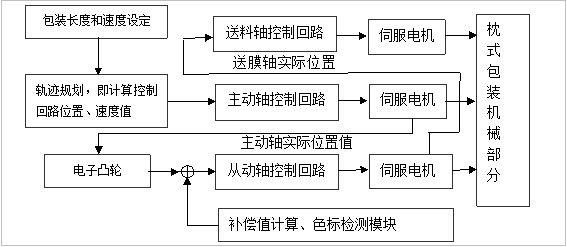
Figure 3. Schematic diagram of the control loop
SHAPE \ * MERGEFORMAT
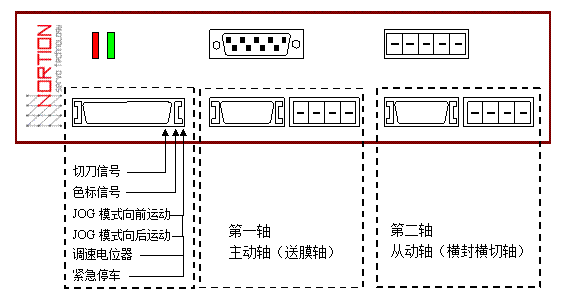
Figure 4. Dual-axis iDrive master / slave axis setup
3.3 System settings and electronic cam
1) Figure 5, Figure 6 and Figure 7 show the debugging interface of this system. This debugging interface is mainly provided for machine manufacturers to use. The debugging of parameters can be realized on a PC, or can be done on a general HMI, or according The customer's specific requirements to customize the software.
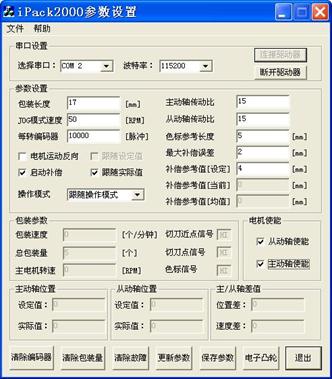
Figure 5. iPack2000 parameter setting interface
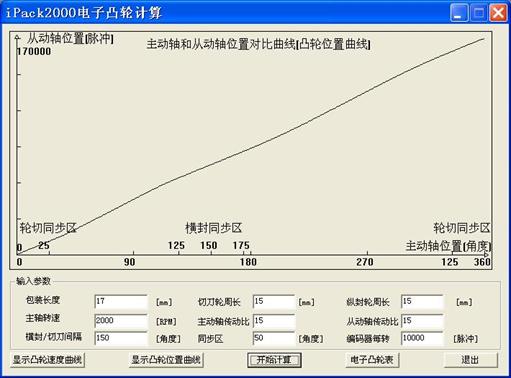
Figure 6. iPack2000 electronic cam calculation (cam position curve)
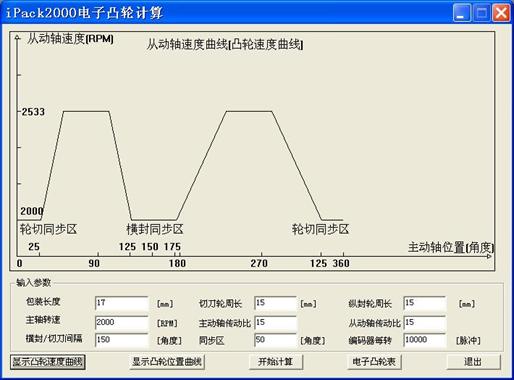
Figure 7. iPack2000 electronic cam calculation (cam speed curve)
Figures 6 and 7 show the calculation of the iPack2000 electronic cam. Figure 6 shows the comparison curve of the position values ​​of the master axis and the slave axis, where the abscissa is the master axis position value and the ordinate is the slave axis position value. Figure 7 shows the speed curve of the driven shaft in a packaging section. It can be seen that there are two speed synchronization areas, which are the horizontal seal synchronization area and the cross-cut synchronization area. For common heat sealing and hot cutting processes, only one synchronization zone is needed.
3.4 Calculation of color scale compensation
l Compensation calculation
The calculation of the compensation amount mainly depends on the color mark signal and the cutter near-point signal, as shown in Fig. 8. The compensation measurement value is L = L1 + L2 / 2, that is, the compensation measurement value is the number of pulses of the motor encoder between the cutter near-point signal and the color mark signal plus half of the color mark width.
After obtaining the compensation measurement value, the system calculates the net compensation value again. The method is:
Net compensation value = compensation standard value-compensation measurement value;
l Compensation area
After the net compensation value is obtained, the motion speed of the driven shaft needs to be compensated. In order to ensure the stability of the conveying speed of the package during the transverse sealing and transverse cutting, it is necessary to avoid the synchronization area of ​​the driving shaft and the driven shaft for compensation. The setting of the compensation area is shown in Figure 9.
SHAPE \ * MERGEFORMAT
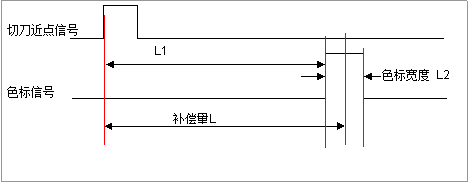
Figure 8. Compensation calculation and compensation point selection instructions
SHAPE \ * MERGEFORMAT
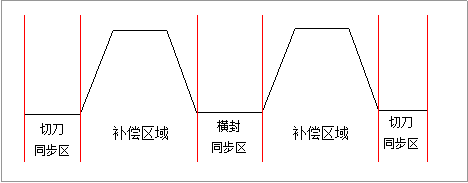
Figure 9. Compensation area description
3.5 Adopt cutter near point signal or software method to avoid false detection of false color mark signal
As can be seen from the above system workflow, the system will continuously detect the color mark, and compensate the operation of the film feeding shaft according to the detected error to ensure the position of the transverse sealing and transverse cutting. However, there may be contamination or other printed patterns on the packaging film, which may easily cause false detection of color mark detection. To solve this problem, the cutter near-point signal is introduced into the system, and this signal is used as the starting signal for color mark detection. The color mark signal will not be detected in areas outside this range, as shown in Figure 10.
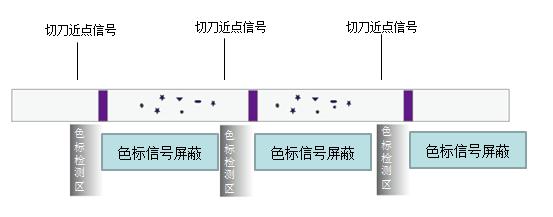
Figure 10. Schematic representation of color mark detection area
It should be noted that the function of defining the color mark detection area by shielding the color mark signal can also be realized by pure software, which makes the system more concise. That is, based on the cutter sensor signal (not the cutter near-point signal), the color mark signal detection is started after a certain length of the cutter action is set, so as to achieve the effect of shielding the color mark detection interference. The specific setting position length can be calculated according to the length of the package and the relevant dimensions of the device, and is completed by setting relevant parameters.
4 Conclusion
The use of iPack2000 to build a multi-axis pillow packaging control system has the following advantages:
(1) The system is simple and compact.
Because iPack2000 has built-in electronic cam and vehicle logo capture and compensation functions, and the intelligent driver can be directly connected to the HMI, the system construction is more concise and convenient.
(2) Significant price advantage and performance advantage
Since the electronic cam, synchronization, and following functions are built into iDrive, the system's cam function does not need to be performed by the upper PLC, and the synchronization and following functions are realized directly at the driver level. The system's response speed and control accuracy have been significantly improved . The original PLC can directly omit or select a PLC with a smaller function, thereby achieving the purpose of saving investment.
The multi-axis servo pillow packaging machine control system iPack2000 based on the intelligent servo technology with independent intellectual property rights in China adopts a bus-type control architecture, built-in motion controller, built-in electronic cam, multi-axis synchronous flying shear, multi-axis following, high-speed color mark real-time compensation , Built-in PLC to complete I / O function, all motion control is completed at the level of servo drive, the system responds quickly, the structure is simple, the scalability is strong, it can be widely used in various multi-axis pillow packaging machines, the cost is low, and it is less than imported products The cost exceeds 50%, and will gradually become the mainstream solution of the pillow packaging industry control system.
As we all know that the parents all over the world pay more attention on children education, so more and more businessman do education laptop deals, therefore education laptop is becoming one of the most important fields no matter on customizing laptop or brand one. There are different series according to students ages, 14 inch celeron windows 10 education laptop for elementary students, 15.6 inch j4125 intel education laptop for middle or high school students or normal business jobs, 15.6inch 10th or 11th windows laptops for students in college or professional business or online teaching, etc. Besides, 15.6 inch 10th with 2gb graphics Programming Laptop or 16.1 inch i5 i7 i9 9th HQ GTX 1650 windows laptop for programming also available.
Other Type devices, like Yoga Laptop , Custom All In One PC, High Performance Mini PC or Android Tablet also available.
So you just need to share the education laptop price and parameters matched prefer, then right valuable information provide directly for you.
You are always welcome whatever only consult or have purchase plan recently.
Education Laptop,Education Laptop Deals,Windows 10 Education Laptop,Top Rated Student Laptops,Intel Education Laptop
Henan Shuyi Electronics Co., Ltd. , https://www.shuyilaptops.com